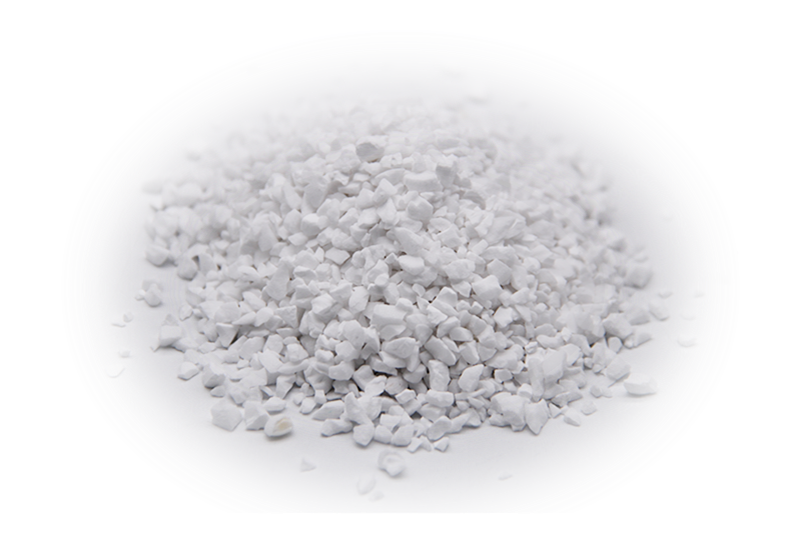
In the world of refractory materials, the process of sintering is crucial for achieving the desired properties of strength, durability, and heat resistance. This process involves compacting and heating raw materials to form a solid mass with improved physical and chemical properties. One key material that is now benefiting from advanced sintering technology is boron carbide.
Boron carbide is a superhard material with a wide range of industrial applications, including use in refractory materials. Its high hardness, low density, and excellent chemical resistance make it an ideal component for creating high-quality refractory products. However, the traditional sintering process for boron carbide has often been challenging, leading to limitations in the quality and performance of the final products.
Recognizing the need for advanced sintering technology, Henan Junsheng Refractories Limited has made significant strides in revolutionizing the production of boron carbide-based refractory materials. With over 20 years of experience in the industry, the company has established itself as a leading manufacturer and trader of refractory and abrasive raw materials, delivering high-quality products to various industrial sectors.
Utilizing advanced science and technology, modern equipment, and strict process management and control, Henan Junsheng Refractories Limited has developed a series of high-quality refractory materials that are highly dependent on the innovative sintering technology for boron carbide. This breakthrough has not only improved the overall performance of their products but has also set a new standard for the industry as a whole.
The advanced sintering technology for boron carbide involves carefully controlled heating and consolidation processes, allowing for the efficient and uniform densification of the material. This results in refractory products with enhanced mechanical strength, thermal stability, and chemical resistance, meeting the stringent requirements of high-temperature industrial applications.
One of the key advantages of this advanced sintering technology is the ability to tailor the properties of boron carbide-based refractory materials to meet specific customer needs. Whether it is improving wear resistance, thermal conductivity, or corrosion resistance, Henan Junsheng Refractories Limited can now offer customized solutions that were previously unattainable through traditional sintering methods.
Furthermore, the enhanced properties of the sintered boron carbide-based refractory materials have opened up new possibilities for their use in challenging environments, such as metal smelting, ceramics manufacturing, and aerospace applications. The improved durability and performance of these materials have garnered significant interest from a wide range of industries looking to optimize their processes and reduce maintenance costs.
Henan Junsheng Refractories Limited's investment in advanced sintering technology for boron carbide has solidified its position as an industry leader and innovator. The company's dedication to research and development, coupled with its commitment to delivering top-notch products, has raised the bar for refractory material manufacturers worldwide.
Looking ahead, the company is focused on further refining its sintering technology and expanding its product line to cater to evolving customer demands. By staying at the forefront of technological advancements, Henan Junsheng Refractories Limited is poised to continue driving the advancement of refractory materials and contributing to the success of industries that rely on high-performance, heat-resistant materials.
In conclusion, the integration of advanced sintering technology with boron carbide has significantly elevated the quality and performance of refractory materials, thanks to the pioneering efforts of Henan Junsheng Refractories Limited. As the company continues to push the boundaries of what is possible in the industry, the future looks promising for the development of even more innovative and effective refractory products.