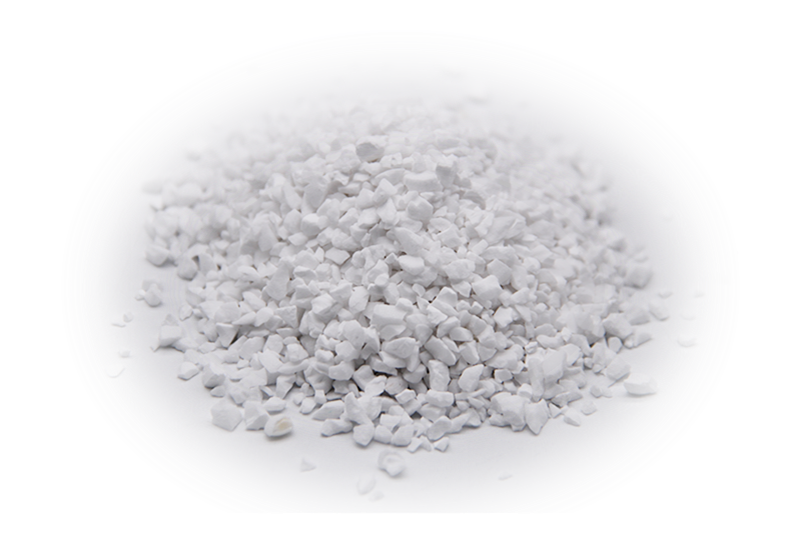
Zirconia and aluminum oxide are both widely used as abrasives and refractory materials due to their high durability and resistance to heat and corrosion. However, in recent years, zirconia has emerged as a strong competitor to aluminum oxide due to its superior properties.
Zirconia, also known as zirconium dioxide, is a white crystalline oxide of zirconium that exhibits high strength, toughness, and resistance to wear and corrosion. These properties make it an ideal material for applications where high performance and reliability are essential, such as in the production of cutting tools, grinding wheels, and refractory linings.
Compared to aluminum oxide, zirconia offers higher hardness and fracture toughness, which translates to improved cutting and grinding capabilities. Additionally, zirconia has a higher thermal conductivity, allowing for better heat dissipation during high-speed operations, leading to reduced thermal damage and longer tool life.
Furthermore, zirconia has a unique phase transformation mechanism that enables it to undergo a reversible change in structure under stress, known as transformation toughening. This property allows zirconia to resist crack propagation and retain its strength and integrity even under extreme conditions, making it highly desirable for demanding industrial applications.
Despite these advantages, aluminum oxide remains a popular choice for many applications due to its lower cost and versatile performance. However, as industries continue to demand higher efficiency and productivity, the superior properties of zirconia are driving its increased adoption in various sectors.
Henan Junsheng Refractories Limited has been at the forefront of harnessing the potential of zirconia by developing and producing a range of high-quality zirconia-based products tailored to meet the specific needs of their customers. Through their advanced manufacturing processes and rigorous quality control, the company has been able to deliver zirconia materials that offer exceptional performance and reliability in the most demanding applications.
It is important to note that both zirconia and aluminum oxide have their distinct advantages and limitations, and the choice between them ultimately depends on the specific requirements of the application. While zirconia excels in high-performance cutting and grinding operations, aluminum oxide may be more suitable for general-purpose abrasion and refractory applications.
As industries continue to push the boundaries of performance and efficiency, the ongoing development and innovation in zirconia and aluminum oxide materials are expected to drive further advancements in manufacturing and technology. Henan Junsheng Refractories Limited, with its commitment to excellence and innovation, is well-positioned to play a pivotal role in shaping the future of refractory and abrasive materials.
In conclusion, the competition between zirconia and aluminum oxide reflects the relentless pursuit of excellence in the industrial and manufacturing sectors. As companies strive to enhance productivity and performance, the role of advanced materials such as zirconia will continue to expand, offering new possibilities for innovation and progress. Henan Junsheng Refractories Limited is poised to lead this charge, driving the advancement of zirconia and other high-quality refractory materials to meet the evolving needs of the industry.